The color transformation of Diesel Particulate Filters (DPF) upon coating with precious metal catalysts varies significantly between cordierite and silicon carbide materials. For cordierite-based DPFs, the originally pure white carrier surface adopts a grey hue after catalyst coating, directly attributable to the precious metal application. Conversely, silicon carbide DPFs exhibit an opposite color transition, presenting a white surface post-coating compared to their uncoated state. This contrasting behavior stems from the inherent material properties and distinct coating processes of these two substrates.
Cordierite DPFs offer economic advantages with their low cost and lightweight construction, making them particularly suitable for low to medium load vehicles. However, their performance is constrained in high-temperature and high-load operational conditions. In contrast, silicon carbide DPFs demonstrate superior thermal resistance and mechanical strength, rendering them ideal for heavy-duty applications, albeit at a higher cost and increased weight.
Regarding Diesel Oxidation Catalysts (DOC), the coated versions typically display a characteristic brown coloration at their ports. These modern emission control devices are specifically designed for contemporary diesel vehicles, effectively reducing harmful emissions. Nevertheless, their implementation comes with increased costs and demands higher fuel quality standards. The uncoated DOC carriers maintain a base color spectrum ranging from dark gray to silver gray.
Selective Catalytic Reduction (SCR) systems present a diverse color palette based on their catalytic composition. Copper-based molecular sieve SCR ports are distinguished by their green coloration, while vanadium-based variants appear yellow. Iron-based SCR systems are characterized by dark gray or black ports. Similar to DOC carriers, the uncoated SCR carriers maintain a base color of dark gray or silver gray, providing a neutral backdrop for their subsequent catalytic treatments.
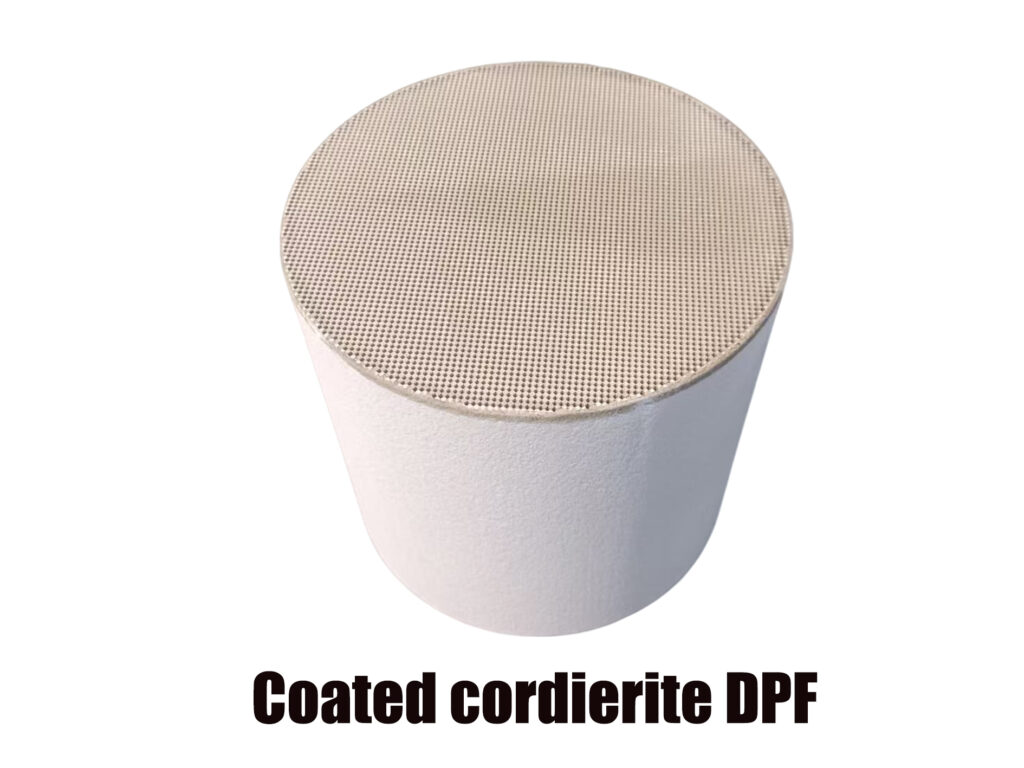
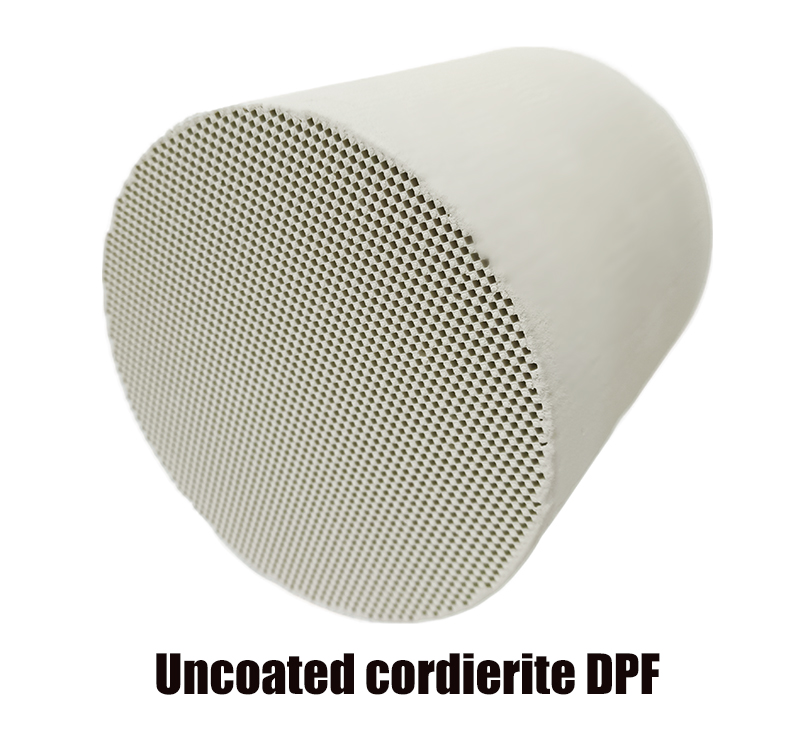
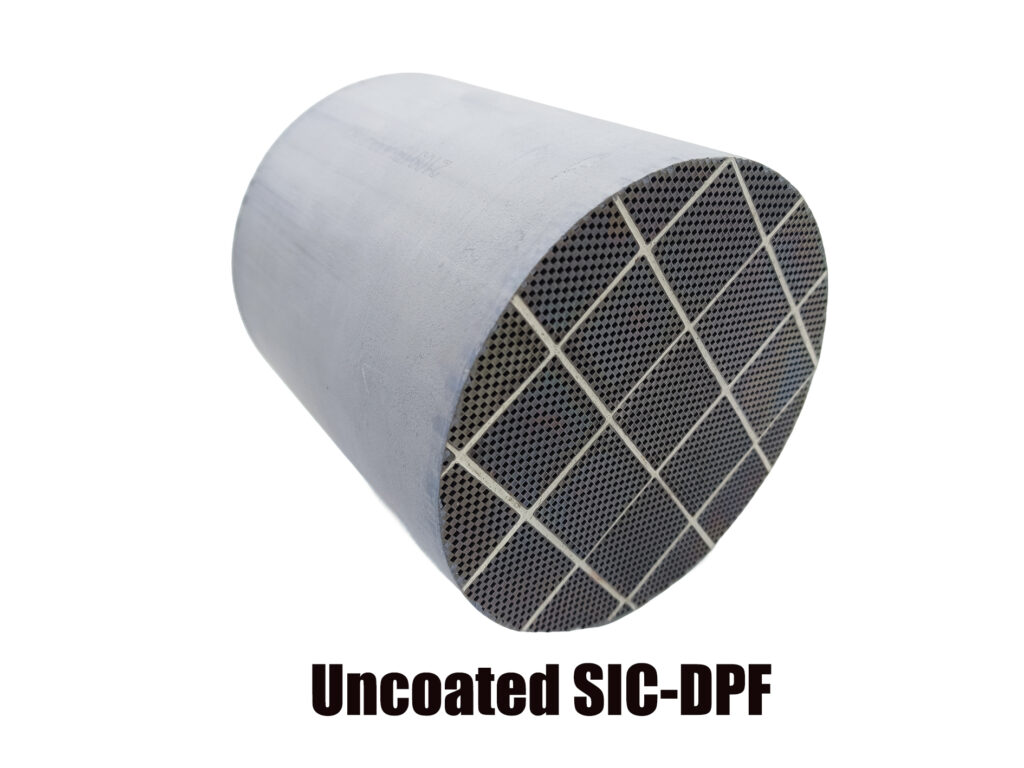
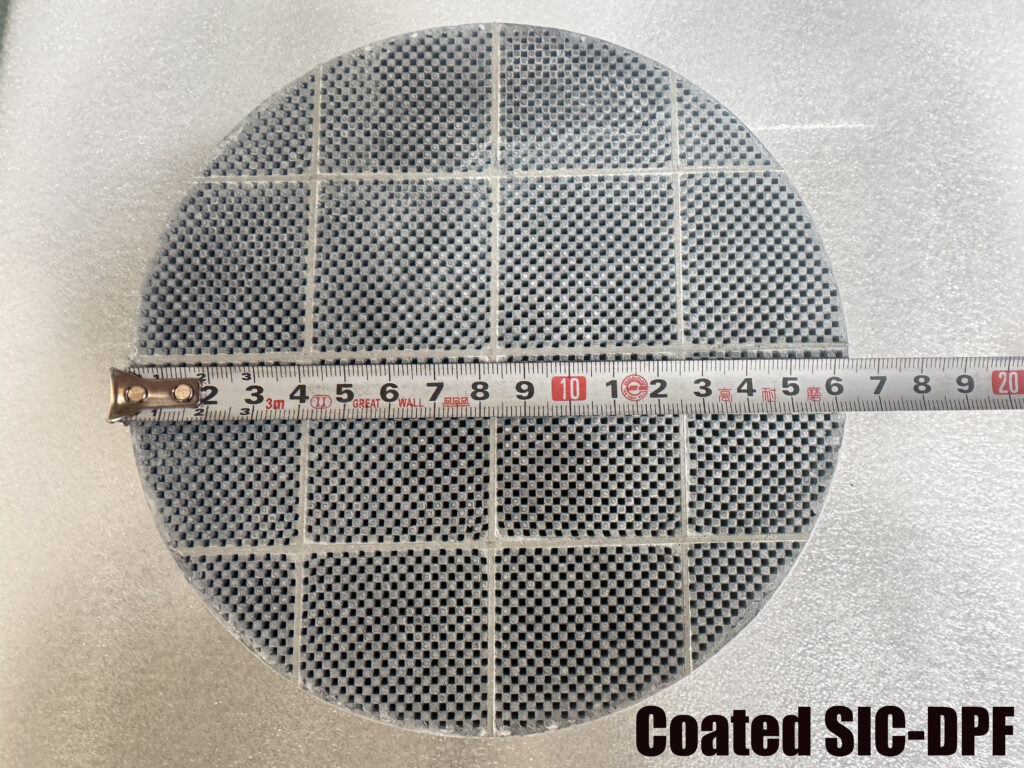
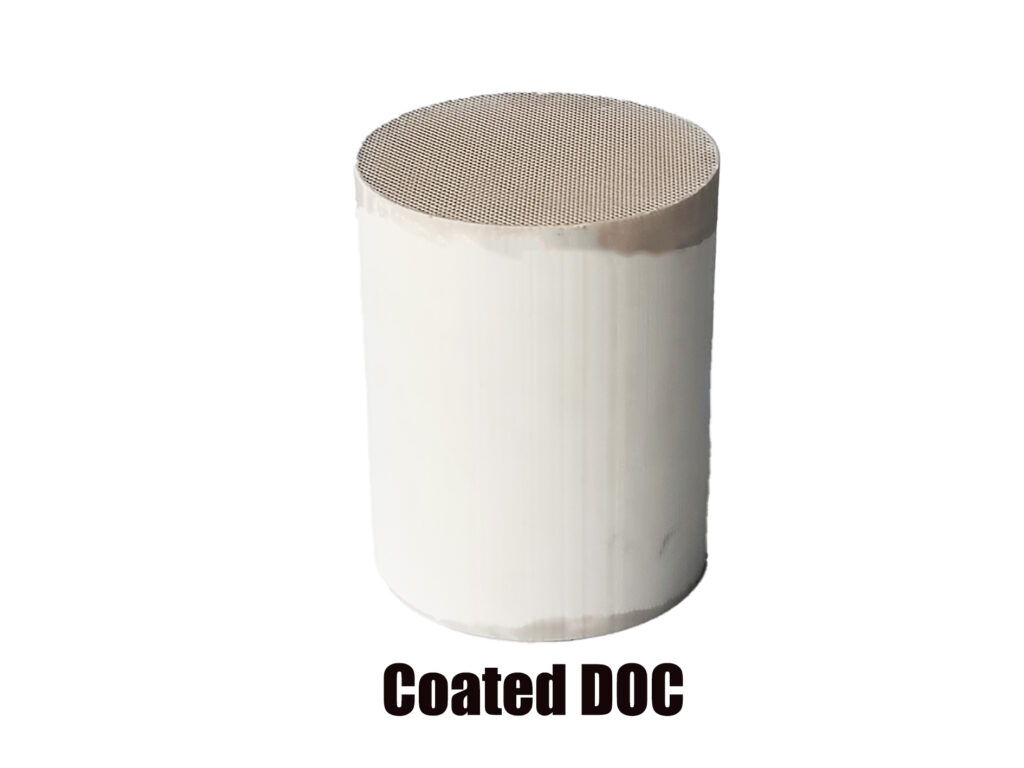
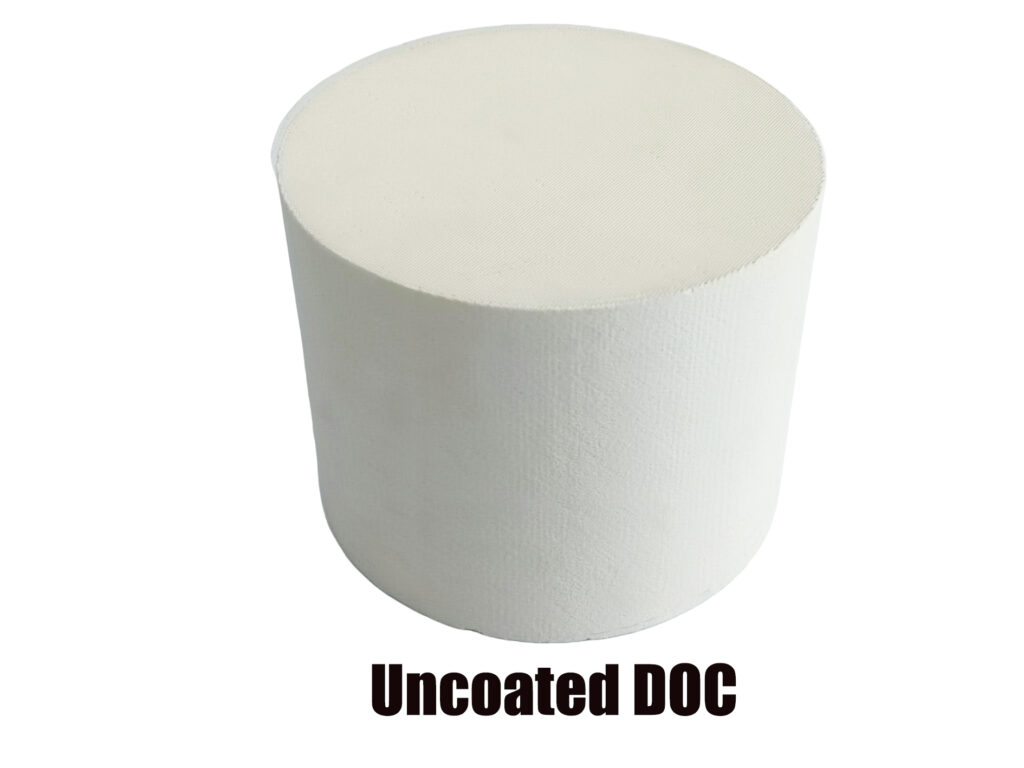
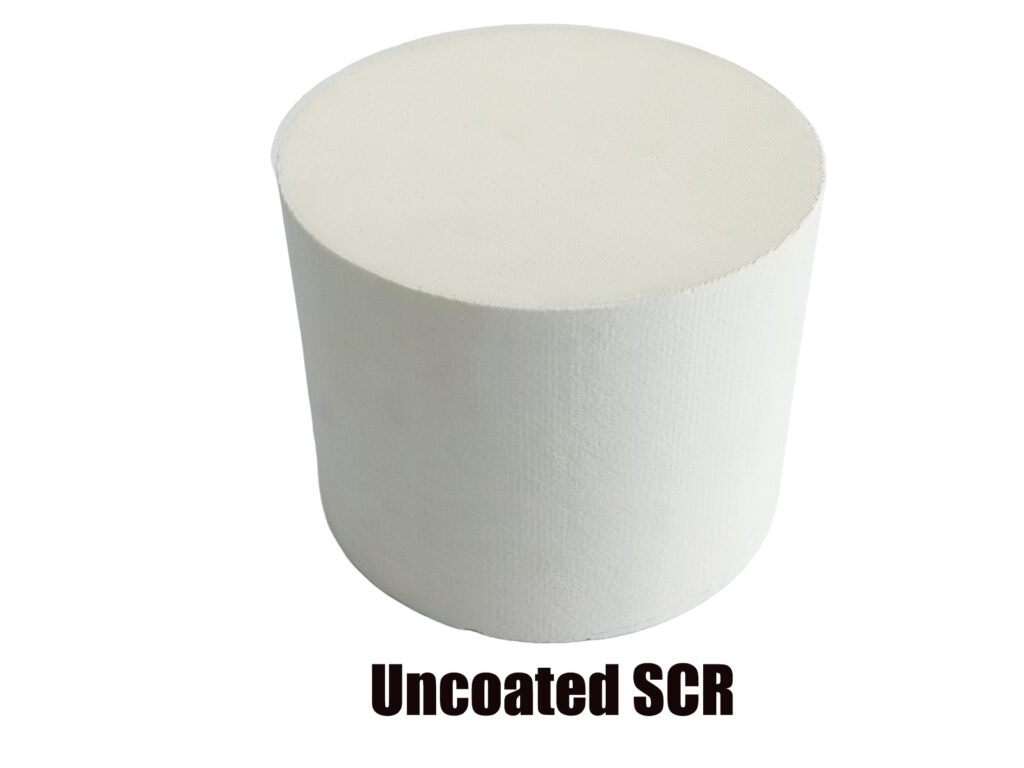
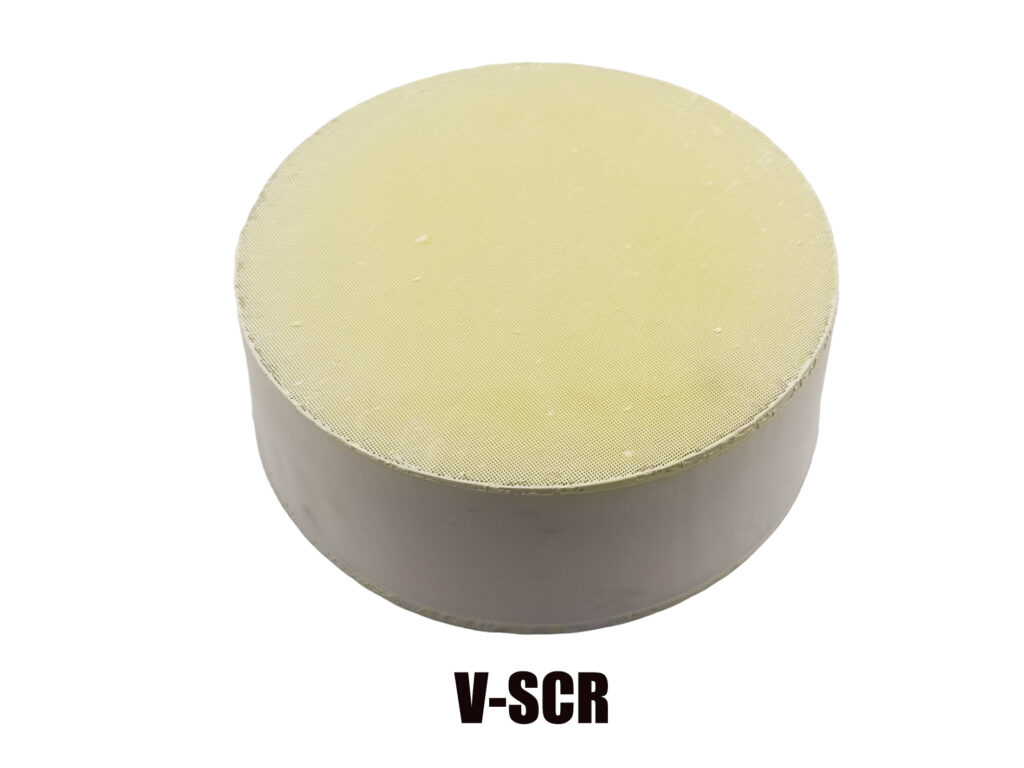
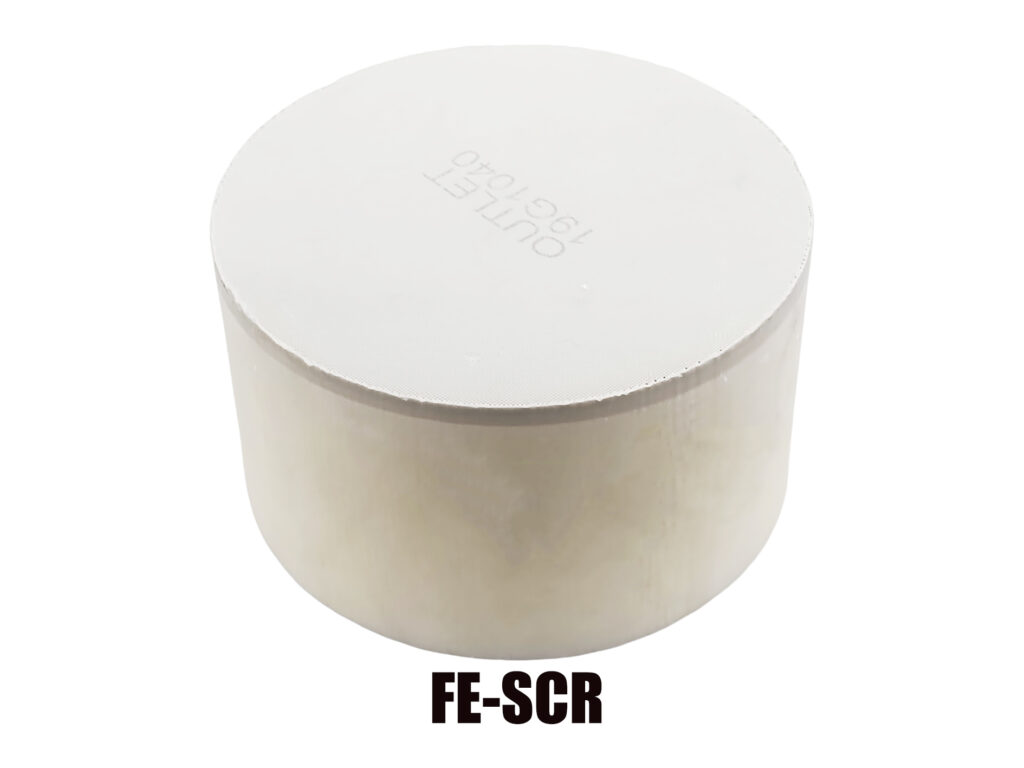
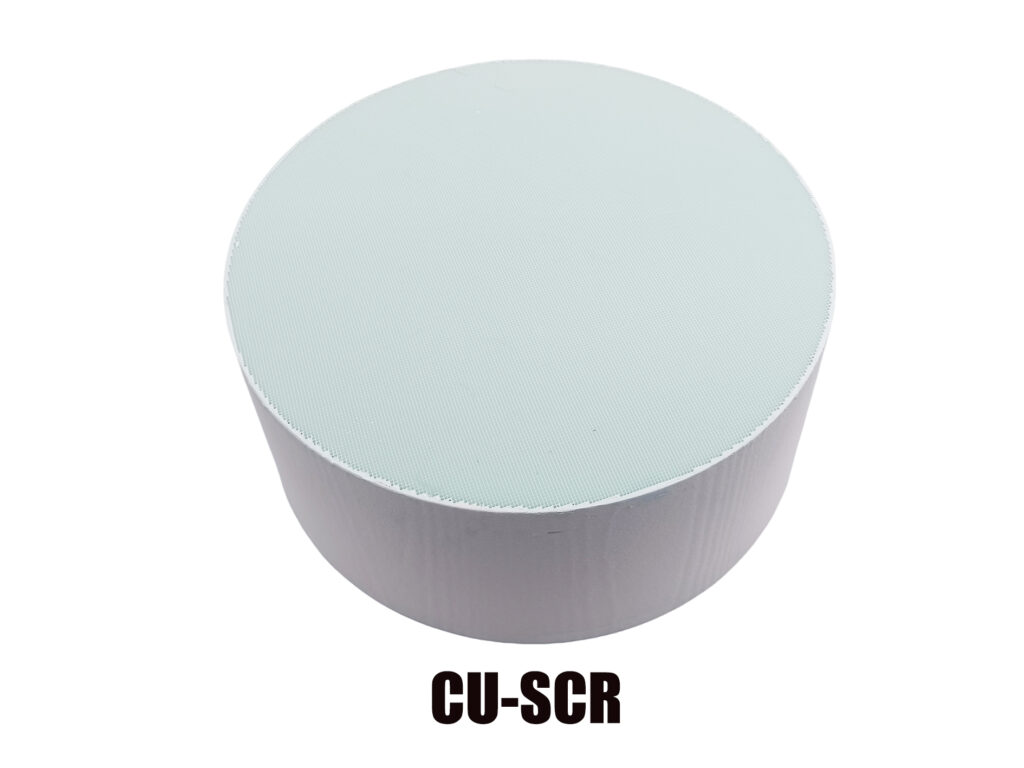