The patterns on the two ends of a Diesel Particulate Filter (DPF) substrate are designed differently to optimize filtration performance, airflow distribution, and mechanical strength. Here are the key reasons:
- Functional Differences Between Inlet and Outlet Ends
- The inlet end typically has a **larger pore size or more open pattern, allowing exhaust gases to enter more easily while preventing clogging by large particles and reducing backpressure.
- The outlet end features a finer or more enclosed pattern, ensuring trapped particulate matter is effectively retained and preventing emissions escape.
- Optimized Airflow Distribution
The asymmetrical patterns help distribute exhaust gases evenly across the substrate, avoiding localized high or low flow rates, which improves filtration efficiency and extends DPF lifespan. - Thermal Management Requirements
The inlet pattern may promote turbulence to enhance heat transfer, aiding rapid temperature rise during DPF regeneration, while the outlet end maintains stable flow to prevent sudden cooling. - Mechanical Strength and Durability
The inlet end faces higher thermal and particle impact stresses, requiring a more robust structure, whereas the outlet end can have a simpler design due to cleaner exhaust flow. - Manufacturing and Cost Considerations
The differing patterns may balance production complexity and cost—for example, simplifying the outlet end to reduce material usage.
Conclusion: The distinct patterns on each end of a DPF substrate result from a careful balance of fluid dynamics, filtration efficiency, and durability, ensuring reliable performance under demanding conditions.
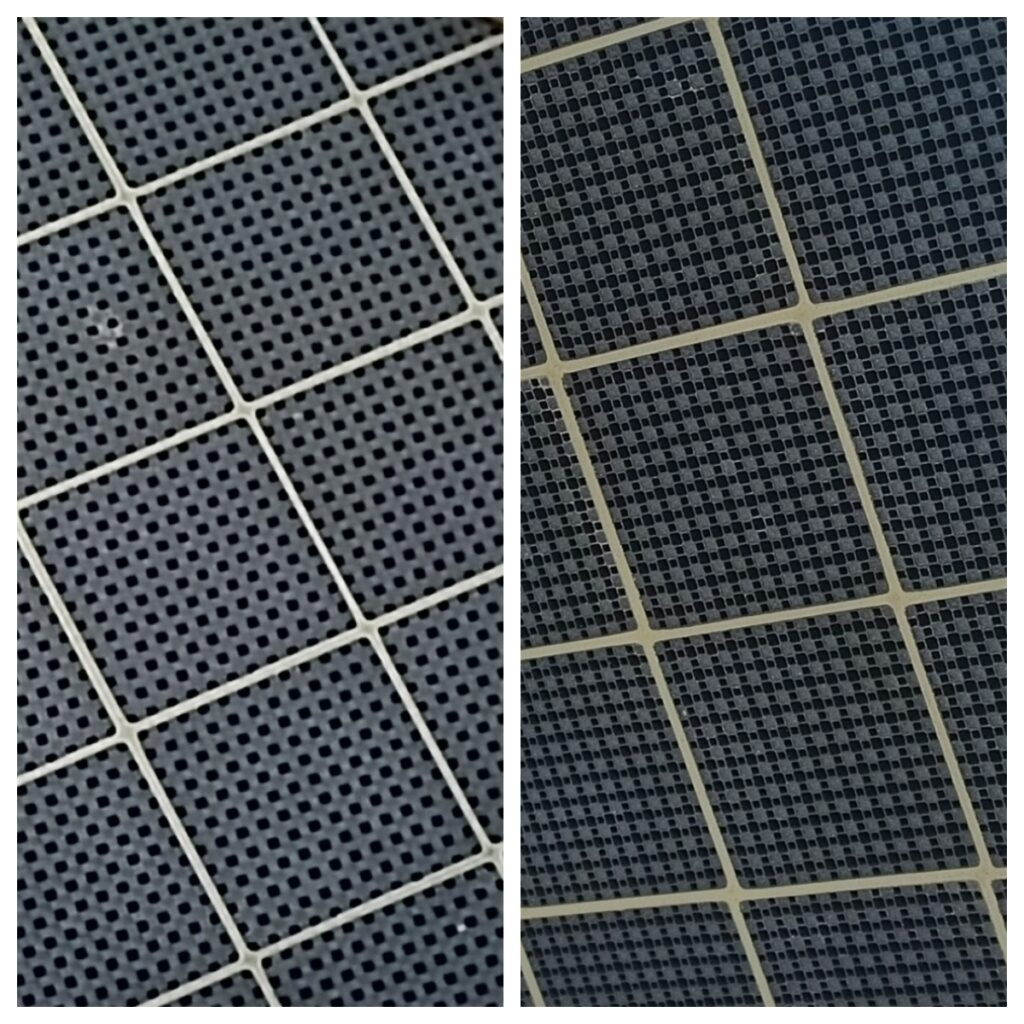